說明
因為長期從事工廠管理實踐和研究,所以積累一定的工廠管理的相關經驗和知識,形成了自己的知識體系和判斷依據。同時,也經常會在朋友圈中看到很多關于工廠管理的一些觀點,有點感慨。此文,不針對任何人,僅僅是對觀點本身的解讀。
1、觀點1:按照客戶需求TT投產
這個觀點至少是非常不全面,也可以說,僅僅可以適應汽車(整機)零部件行業,汽車零部件的后裝行業都不適應。
但是,在實際場景中,客戶需求是隨機波動,相比客戶需求,產出能力(產能)是相對固定的,變動范圍極其有限。
又,一般生產過程可以細分為離散、半離散和連續三個。而生產計劃會采用三種方式:追逐式(產出=需求)、平衡式(產出=產能)和混合(產出=需求=產能)。相對應的是,離散的生產過程,往往是追逐式生產計劃(產出=需求),平衡式(產出=產能)和混合(產出=需求=產能)是不可能實現的。
就是在離散生產過程的追逐式(產出=需求)中,也不可能做到按照客戶需求TT來組織生產。
其原因是:首先是產出的相對剛性與需求的柔性有沖突。一般一個機械、服裝、家具和家電的設施、設備、人員、工裝模具等等均是有限資源,其產出是相對剛性的。而需求存在需求的時間、需求的品種的高度柔性。不同的產品,對產能的需求不同,很難實現客戶需求與產能節拍的同步。
可以說,實際場景下,按照客戶需求TT來投產,既不經濟,還不現實。
2、觀點2:庫存是萬惡之源
可以在書、朋友圈中N多人宣傳,庫存是萬惡資源。一般都認為庫存越低越好。果真如此嗎?其實不然啊。
首先,里特定律WIP=TH*CT告訴我們,適量的WIP是確保產出的前置條件。有了WIP才有了TH。對于高速公路相關部門而言,節假日才是收錢的高峰期(免費狀況除外),因為在制品多(路上車多),TH(閘口過的車多)高啊,CT(犧牲了開車者的時間,長)自然會長。
其次,因為“墨菲”的存在,在分叉點、合流點、順流節點上必然存在庫存
N多的人,想消除“墨菲”,但是“墨菲”永遠不可能被消除。從事物的本源看,因為有量子效應的存在(薛定諤的“貓”,可以腦補一下《時間簡史》、《果殼里的宇宙》等),看看老兵多炮轟接可以知道(有經驗的老板,一般把自己藏在上一個炮彈坑里,因為沒有那么精準的跑,落在同一個彈坑中)。
因為需求的變動性,因為供應的變動性,所以必然需要在合流點備庫,以實現齊套;必然在分叉點備庫,以響應需求變動;在順流節點備庫(半導體行業尤其如此),以確保產出。
從以上分析看,庫存不是萬惡之源,是物料流動性過程中的必然保障,是促進物流的必要手段。關鍵是如何配置庫存?關鍵是如何在工廠恰當的位置、恰當的時間、配置恰當的數量?
說庫存是萬惡之源,或許是沒有理解工廠的本質?
3、觀點3:把瓶頸作為同步點實現拉動
工廠的投料有三種方式:倒排拉動、順排推動、瓶頸的前拉后推。
一般而言,都喜歡瓶頸的牽拉后推,要不然是倒排拉動,很少有人會喜歡順序推動。但是,在實際的工廠中,可以說肯定沒有瓶頸前拉后推的排程,也很少有純粹的倒排拉動,絕大部分的場景(99%以上)采用了“倒排順投”的方式。
為什么呢?瓶頸的前拉后推太復雜了,現實中無法實現
要實現瓶頸的前拉后推,首先是要識別瓶頸。而識別瓶頸的最佳辦法是實現有限產能(FCS)的預期排程,這個就需要用到一款軟件“APS高級計劃和排程”,至少目前,真正懂APS高級計劃排程的人不多。其次,識別瓶頸的難度很大。要識別瓶頸,需要進行工序級、獨立資源的排程才可以的,Excel是無法實現的。或許有人會說,可以采用簡化的方式來識別個固定瓶頸,自然這個是個很好的方法。關鍵是在大部分場景下,瓶頸是浮動的,不僅在設備上跳躍,也會在時間上跳躍。其三,就是識別了設備和時間維度上的瓶頸,有如何將瓶頸上的工序任務的優先順序(動態的),同步至瓶頸前的設備的工序任務呢?
所以說,要實現瓶頸的前拉后推排程,一般僅僅適應于固定瓶頸場景,非常簡單的場景,才是有效的。《目標》、《速度》描述的是用碳纖維生產飛機機翼、飛機機身的場景,熱處理罐是瓶頸,且是固定的瓶頸,才是可以的。
其實,現場場景中,更多的是以交期(TOC中的SDBR)、庫存水位點作為同步點拉動,并實現齊套投料的方式生產,是“倒排順投”,用提前生產來平衡產能的波動。
4、觀點4:不排程可以高產
工廠績效的最高標準是:交付好(準交率高/交付周期短)、產出高(設備/人員產出率高)、庫存低(庫存周轉率高)。要滿足以上條件,需要做到三個遷就:遷就需求、遷就瓶頸、遷就供應,也就是要實現需求、產能和供應的穩定和同步。
其一,需求、產能和供應的穩定
其實,目前的狀態下,需求的穩定是不可能的(汽車零部件前裝行業,相對比較穩定),別的行業因為產品時尚化和消費習慣、消費渠道的變化,訂單的碎片化(多品種、小批量和定制化)非常嚴重,需求的隨機性增加。
我們只有在產能、供應的穩定性上下功夫,精益生產的N多方法和工具在這個方面可以起到非常好的作用(標準作業、5S、TPM、TQM、多能工等)。用產能、供應的穩定,來響應需求的不穩定。
其二,需求、產能和供應的同步
要實現需求、產能和供應的同步的唯一方法,是預排程。
對需求(預測、銷售訂單、補庫訂單)對物料需求、產能需求進行預期排程,讓物料供應與產能需求匹配、讓產出與需求匹配。
要實現高產出,則需要就瓶頸的產出,前工序為瓶頸工序服務,而增加瓶頸產出最簡單的方式,是減少換型。減少換型則必須要預排程。
要減少庫存(原材料、在制品和成品),則需要根據實際的需求、產能狀況和物料供應投料。僅僅一個物料約束,就需要考慮在制、在庫、在途、采購前置周期四種,還需要考慮訂單量分割、工單任務分割、工序任務分割和工序任務的轉移,還需要考慮各類的后處理時間等時間維度,是一個復雜過程。更是需要預排才是可以的。
預排,哪怕是粗淺的預排,是高效的一個保障。當然,最好是做到“排長鎖短”,既保證長期的優化,更可以保障短期的穩定,還保留了足夠的柔性。
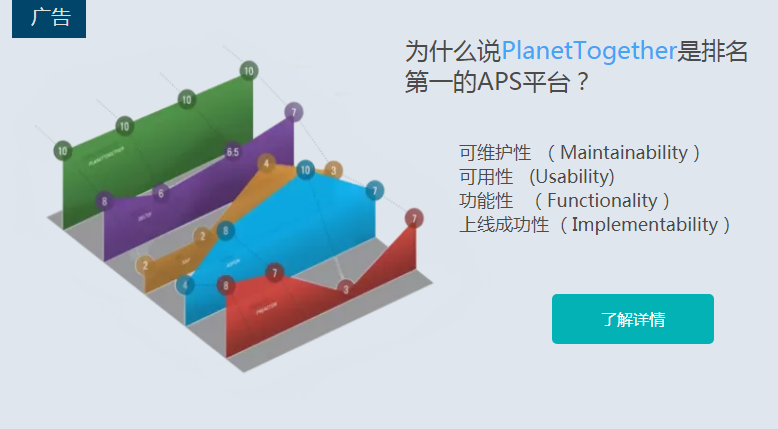