1. 數字孿生機床
機床是制造業中的重要設備。隨著客戶對產品質量要求的提高,機床也面臨 著提高加工精度、減少次品率、降低能耗等嚴苛的要求。
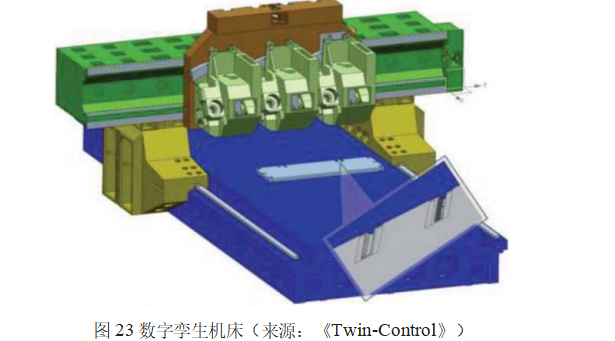
在歐盟領導的歐洲研究和創新計劃項目中,研究人員開發了機床的數字孿生 體,以優化和控制機床的加工過程(圖23)。除了常規的基于模型的仿真和評估 之外,研究人員使用開發的工具監控機床加工過程,并進行直接控制。采用基于 模型的評估,結合監視數據,改進制造過程的性能。通過控制部件的優化來維護 操作、提高能源效率、修改工藝參數,從而提高生產率,確保機床重要部件在下次維修之前都保持良好狀態。
在建立機床的數字孿生體時,利用CAD和CAE技術建立了機床動力學模型
(圖24)、加工過程模型、能源效率模型和關鍵部件壽命模型。這些模型能夠計 算材料去除率和毛邊的厚度變化,以及預測刀具破壞的情況。除了優化刀具加工 過程中的切削力外,還可以模擬刀具的穩定性,允許對加工過程進行優化。此外, 模型還預測了表面粗糙度和熱誤差。機床數字孿生體把這些模型和測量數據實時 連接起來,為控制機床的操作提供輔助決策。
機床的監控系統部署在本地系統中,同時將數據上傳至云端的數據管理平臺, 在云平臺上管理并運行這些數據。
該機床的數字孿生體已經在兩個工業項目中做過驗證。第一個項目來自航空 行業,測試了三臺位于MASA (Logrono,西班牙)的Gepro機床。第二個項目來 自汽車行業,采用位于法國Cleon雷諾工廠的三臺Comau機床進行了驗證。