日本TKR東北工廠的APS案例分享
導入目的
●實現從物料采購到公司最后一步的統一管理
●優化管理體系,提高內部決策速度
●實現整個公司的信息可視化,以達成共識
當Asprova在2008年推出時,為了建立標準系統并實現信息的統一管理,公司對現有的信息系統進行了很大的改進。
其中之一,包括制造業的共同主題,是減少庫存到最低限度,并能夠處理諸如訂單變更,設備故障,其他操作員等不確定因素,以掌握現在的訂單。步驟,何時完成,瓶頸過程在哪里,并探索縮短交貨期和減少庫存的方法。作為解決方案,決定導入生產計劃軟件。
導入計劃軟件的特定目標是自動計劃和歸檔,縮短歸檔時間并及時響應人員和設備的負載。掌握工作流程的時間,管理物料的庫存信息,反饋給生產計劃,并通過可視化實現信息共享。根據這些要求,最終選擇了Asprova。
此外,公司2010年的經營方針是“讓一切都快行動”。針對訂單的變化和不確定性,我們應該盡力快速做出響應并提高計劃速度,這也是選擇Asprova的重要因素之一。
從介紹到正式申請,Asprova的推廣項目遍布整個公司
盡管它是導入的,但實際上,它要花很多時間才能按照Asprova制定的計劃順序進行制造。這是因為Asprova APS系統會根據制造周期和庫存條件進行計劃,而不必按現場輕松工作的計劃順序進行計劃。為此,負責介紹工作的齋藤先生設立了Asprova推廣項目并實施了以下項目。
-通過公司內部指導會議,以介紹的目的和方向,重新審查了工藝單元的設置方法和統一通用方法以及計劃周期。在指導會議上,除了說明Asprova的介紹目的和效果外,還指出為了建立一個完整的系統,制定生產進度表的人員和根據進度表進行管理的人員(材料,生產,產品質量驗證,管理等),按計劃工作的人們之間的相互理解與合作至關重要。
導入時,所有40個操作的原始計劃都將更改為5個操作的簡單計劃。另外,不是每天制定詳細的計劃和說明,而是一周之內制定計劃,然后讓網站自行調整,以便網站自行決定。
積極利用新功能實現信息可視化
最初導入時,首選中試生產線,現在主要用于印刷電路板的組裝部分,這對后續工藝有很大影響。該公司已在現場放置了七臺大型顯示器來顯示甘特圖。將鼠標放在甘特圖上各過程之間的連接線上。很明顯,先前和后續過程的工作何時開始和結束。我們可以考慮制造前后的過程。此外,公司90%以上的材料由客戶提供。通過輸入作為庫存增加或減少而提供的零件的預期狀況,您可以提前知道它們是否足夠。
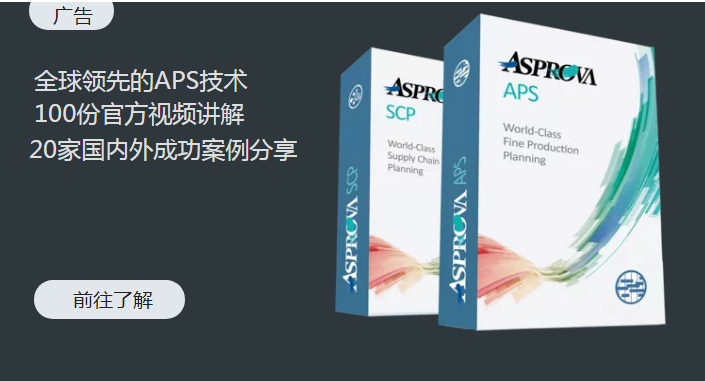
現在,根據用戶零件的供應和交付時間輸入計劃和生產性能,并通過主任和負責人的咨詢來調整基準信息,最終反映出操作過程并掌握工作量。為了獲得真實的結果,我們需要從現在開始。
將來,與從客戶處獲得交貨指示相比,我們將考慮何時需要零件并對訂單進行分類,以作為延長交貨時間的基礎。