深圳共進電子股份有限公司PCBA項目成功上線APS系統
1、基本信息
2、企業信息化應用概況
目前,kyoce的應用信息系統包括orcale ERP、自主開發的MES系統,并與Asprova APS系統有效結合,提高了企業的整體信息水平。
3、項目詳細信息
1. 項目背景
co - operation電子生產模式的特點包括:
(1)批量生產,多品種、小批量,訂單導向生產;
(2)產品結構復雜,設計變化頻繁;生產計劃復雜,產品品種多,更新快;按單定制生產,快速排產;備件品種多,型號多,替代材料和選配材料通用;產品質量可追溯性要求高。
同時,公司的快速發展帶來了PC、MC、調度部門的局部優化和不協調運行,導致手工excel調度過于復雜,成為業務發展的瓶頸,急需導入生產計劃系統。因此,需要一個更先進、更專業的調度系統。三年前,工進電子在國內制造商中選擇了Asprova作為APS系統的供應商。由于內部MES升級和新工廠建設,沒有實施Asprova。一年前,公司對國內外生產廠家進行了二次APS選型。最后,Asprova脫穎而出。
在眾多APS供應商的選擇中,公勁電子非常重視行業經驗和咨詢服務實力。除了專注于全面的解決方案,它還非常重視APS是否真的能推動業務流程的創新,提升ERP &的準確性和及時性;MES系統數據,全面推動其他系統的改進。經過多輪篩選,已有20年歷史的Asprova被國內外知名軟件廠商廣泛使用,最終勝出。
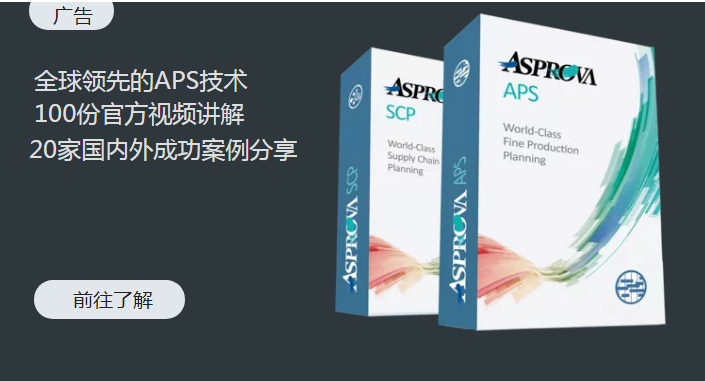
2. APS項目實施目標
(1)實現兩大指標:庫存為0%,訂單交付為100%;
(2)實現產供銷協同:訂單ATP、生產、銷售、庫存跟蹤、生產進度跟蹤、呆滯狀態等平臺統一。
APS的進口范圍包括新橋工廠和太倉工廠,以新橋為中心,成功的一個接一個的復制。
第一階段:主需求計劃(MDS)和主生產計劃(MPS)。根據成品瓶頸工序(試驗)的產線能力和全部交貨要求,估算產能,并進行人員計算,實現準確的ATP和生產均衡。
第二階段:材料成套/材料短缺分析。本文在ERP現有MRP功能的基礎上,主要分析了風險材料、長期主芯片材料嵌套、短期包裝材料短缺、成套交付等問題。
第三階段:詳細的生產計劃(DPS)。基于ERP工作指令,對SMT、dip、gateway、光通信、自制件等工段進行協同工作調度,并將工作指令自動分發到MES,實現無縫集成。
3.項目實施及應用
2014年11月18日開始Asprova的導入和實施。一年后,項目團隊在IT部門的帶領下成功上線,規劃部門主要參與。長期核心全職人力投入約33人,包括銷售、業務、策劃、采購、生產、工藝、物料等部門的兼職參與。截至2015年12月1日,T &W大約是700,VUV的輸入man day是712。
4. 效益分析過程創新成果:
(1)產銷協會合作方式的轉變
APS項目的操作和應用,介紹了MDS主需求計劃的概念,并基于aps-mds產銷合作模式,它克服了傳統生產和銷售會議的弱點,比如提前分析太少,窮人和非標準數據可視化,提高數據分析的能力,使生產和銷售數據系統和實時協作,并大大提高了產銷需求數據管理的規范性。同時,主計劃MPs推動需求數據MDS的持續更新,從之前的一個月產銷協作會議增加到現在的一周,大大降低了數據更新不及時帶來的風險。
(2)電子材料分析的變化
APS電子材料完整性分析模型的使用打破了以往手工分析的局限性,如流程節點繁瑣,手工操作較多,分析時間長。同時,材料完整性分析時間從以前的手工1-4小時/次優化到現在的系統5-15分鐘/次,減少了工作時間,提高了工作效率。同時,APS材料模型的使用也規范了套料原理,整合了套料分析邏輯,減少了PC、MC、倉庫等的人力投入,推動了電子套料分析的變革。
(3)日計劃驅動的生產排程改革
運用aps-dps車間日計劃模型,克服了推送與交付之間存在諸多沖突、日計劃無法鎖定、DPS調整耗時長等缺點。它提供了一個自動調度平臺,集成了復雜的和可變的調度邏輯,并組合了各種業務數據。同時,日調度時間從原來的手工4-6小時/天提高到現在的0.5-1小時/天,調度時間大,工作效率也有了很大的提高。APS系統將日常計劃與生產調度相結合,通過推拉相結合的方式穩定車間的日常計劃,減少了計劃調整次數,減少了人力和生產調度時間。同時,該系統能夠及時收集各種數據,并提供可視化的管理報表,為車間生產管理提供有效的依據。
(4)開放APS+MES智能管理
定期連接Aps-dps模型和MES系統進行數據交互。放棄了傳統的手工查詢性能數據的方法,根據設定的時間點獲取最新的性能信息。同時,系統可以自動獲取研討會的異常數據,并自動計算出計劃成就率,提高有效性,實時和準確的數據,實現自動管理車間的飛躍,并打下堅實的基礎的智能管理研討會。
(5)包裝材料采購/ MC業務整合
在系統上線前,包裝材料分析的處理方法是根據客戶和產品型號指定一名跟單員,然后將MC手工計算結果傳遞給采購人員,經過反復確認后進行回復。整個過程既耗時又低效。系統上線后,MC只需要將系統計算出的整套結果發送給采購方,采購方可以配合供應商跟進材料的交付。同時,人工計算包裝材料需要1小時/ 10人,而系統只需10-15分鐘/ 1人,大大減少了MC跟單人員,提高了工作效率,也使得功能轉移到采購。
(6)物資L / T標準化管理
APS系統使用前,電子材料L / T未能及時維護或維護不準確,平均L / T為46天,嚴重影響了總體規劃的安排。同時,也存在沒有L / T更新計劃,沒有專人跟進的缺點。APS系統克服了上述缺點,將平均/ t時間縮短至28天。采購管理也強調了信用證的重要性。
(7)系統發布規劃指令
利用APS,系統自動分發MDS和MPs,將DPS計劃自動分發到MES系統,消除了傳統的郵件傳遞形式,實現了crm-aps - erp-mes數據的實時共享。
為生產計劃的系統化、可視化、透明化管理搭建了平臺,發揮了關鍵作用。
應用效果:
(1)計劃管理系統化+自動生成APS系統實現了從人工調度到系統調度再到自動調度的跨越。從最初的人工調度交叉口少、協調能力差,到現在系統自動調度交叉口多、協調能力強,不斷提高調度精度。實現了計劃管理模式的跨越式發展,全面提升了管理水平。
(2) APS系統上線前,計劃調度模式為4人/周,6人/日。系統上線后,調度角色合并。主計劃員、PCBA和網關計劃員各減少1人。工作效率(PC工時)提高50%,工作時間縮短5-8h /天。同時,物控部采用APS系統,減少2人,提高工作效率(MC工時)90%,縮短工作時間9h /人日。
(3)提高了SMT載荷計算的準確性。通過APS系統自動導出和計算SMT貼片,準確計算MPs貼片負荷,為計劃人員判斷SMT生產能力瓶頸提供依據,并可直接復制到excel中。將SMT載荷計算的精度提高到100%。
(4)計劃發布的標準化程度提高了APS生產計劃和MES同步實現全面控制生產過程,改變了歷史,原計劃無法控制生產過程,并使計劃發布的標準化程度增加到100%。在生