10.3工藝執行與管理
生產跟蹤包括為企業資源計劃作生產響應準備的一系列活動,如總結和匯報關于產品生產中人員 和設備的實際使用、物料消耗、物料生產以及其他如成木和效益分析需耍的有關生產數據信息。生產跟 蹤還向詳細生產排產、以及更高層的企業生產計劃提供反饋信息,以使各層計劃能根據當前情況進行 更新。
數字化車間的生產跟蹤應能動獲取生產相關數據,統計產品生產中各種資源消耗,并反饋給相關 功能/系統/或部門。生產相關數據的獲取來源,包括從數字化接口(數字化設備或工位)直接采集到的, 或者經過其他功能模塊加工過的
10.3.1信息集成模型
工藝執行與管理信息集成模型如W 5所示,主要包括工藝執行與工藝管理兩部分。工.藝執行由車 間子計劃/物料清單生成、派工單生成、作業文件下發等構成,工藝管理由工藝權限管理、工藝變更管理、 可視化工藝流程管理等構成。工藝執行貫穿于計劃、質量、物流、設備等全生產過程中;工藝管理功能可 以在PDM、ERP、MES等相關系統中實現,工藝文件以計算機系統可識別的數據結構呈現。
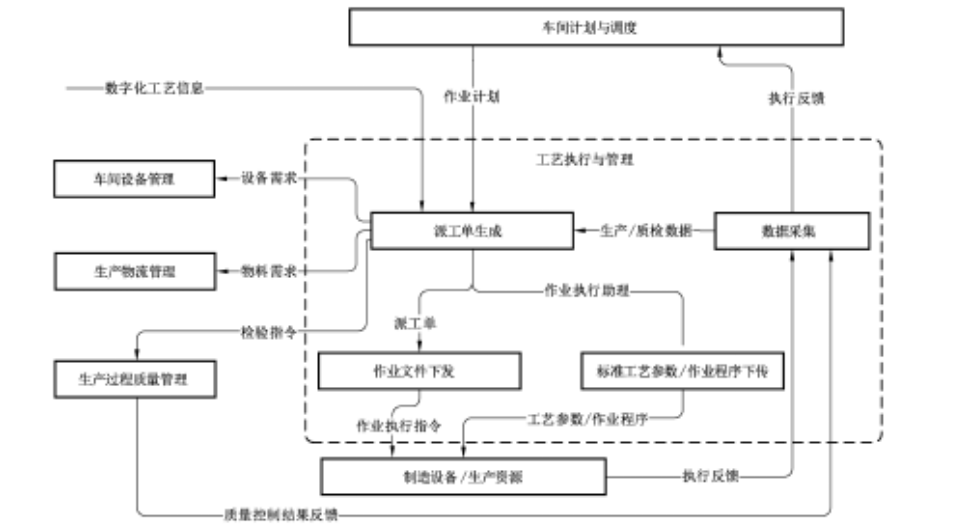
圖5工藝執行與管理信息集成模型
10.3.2功能要求
工藝執行
通過工藝的數字化與車間系統的網絡化,實現作業文件、作業程序自動下發和標準工藝精準執 行;通過生產和質檢數據、現場求助信息采集,反饋工藝執行實時狀態和現場求助信息,實現產品生產工 藝的可追溯與現場求助的快速響應。具體功能包括:
——物料清單生成
根據產品BOM與作業計劃,自動分解生成物料清單,實現生產計劃細分、物料提前備料、工序流轉動采集、工位物料智能化配送等。
——派工單生成
根據生產工藝過程,將車間子計劃分解為各工序的派工單。各工序根據產品BOM、生產工藝過 程、日派工單實現生產前物料備料,車間根據產品BOM、生產工藝過程、標準工時等實現各派工單智能化調度。
—作業文件下發
將各種工藝卡、工藝圖紙、作業指導書等作業文件自動下載到各作業工位終端,現場作業人員可通 過工藝編碼或生產計劃號、工單號實時查詢標準工藝參數、標準質檢工藝、作業指導等工藝信息。
——標準工藝參數、作業程序下傳
通過以太網或總線方式將標準工藝參數自動下發到對應機合,防止由于人為因素導致現場機臺工 藝參數設置錯誤。
作業程序可以A動下傳到現場數字化裝備實現自動加工或裝配等作業。
——數據采集
進行工藝信息在線交互式瀏覽、物料校驗及開工條件檢查;
實時記錄和上傳生產現場出現的工藝技術問題和處理方法;
實時采集生產過程中的工藝參數,向質量控制系統提供生產、質檢數據,實現生產過程質盤預膂,并 通過與生產現場可視化管理系統等進行集成,實現預II信息及時發布;
求助終端實時采集生產求助信息,向生產現場可視化管理系統提供現場求助信息,以便現場作業工 位獲將快速響應;
及時將作業指令狀態信息與作業工位狀態信息向系統反饋。
工藝管理
數字化車間應實現以工藝信息數字化為基礎,借助一體化網絡與車間作業工位終端實現無紙化的 工藝信息化管理;并以可視化下作流技術,實現制造流程再造、工序流轉和調度的數字化管控以及工藝 紀律管理。具體功能包括:
——工藝權限管理
工藝執行權限主要實現組織結構管理、人員管理、訪問規則管理等。一般情況下,組織結構由 Group(組別)、Rde(角色)、User(用戶)和Person(人員)構成。通過訪問規則的定義,來實現對用戶操 作權限的控制,控制用戶、角色、工作組對數據倉庫或具體文檔的操作權限。
根據崗位職責要求進行相應權限分配,對應授權人員可進行相關工藝的上傳、下載、查詢、修改等。
——工藝變更管理
主要實現工藝變更、工藝優化數據版木管理等。工藝變更應符合標準變更工作流程以及控制、跟蹤 機制,結合產品數據的狀態管理,可以在規范管理更改過程、保證更改的可追溯性的M時,提供準確、及 時的更改傳遞機制,保證更改結果的正確性和一致性。
——可視化工藝流程管理
通過可視化工藝流程實現工序間流轉管理,并對工藝流程中各工序點進行M性設置,快速實現數字 化車間生產流程再造,實現數字化車間生產工藝流程快速切換。
棗作業文件管理
作業文件包栝生產流程工藝、工藝卡、工藝圖紙、質檢工藝標準卡、標準工藝參數卡等,并以版本號 區別。
——作業程序管理
作業程序通過工藝編碼或生產計劃號、工單號與數字化裝備關聯,并以版木號區別。
——工藝優化管理
對采集的機臺工藝參數的實際值或質檢數據,進行統計、分析、預膂,實現工藝優化。
——生產求助管理
工位上作業人員針對工位發生的各種問題發出求助呼叫信息,上傳生產現場可視化管理系統,可觸 發聲光報警、顯示終端、廣播等,提示相關人員注意,以便及時處理問題。